Thermodynamics 2
By : Asad Ali Arshad
A Nozzle is a duct of smoothly varying cross-sectional area in
which a steadily flowing fluid can be made to accelerate by a
pressure drop along the duct.
E.g., nozzles are used in steam and gas turbines, in jet
engines, in rocket motors, in flow measurement, in
injectors, in ejectors etc.
Diffuser: When a fluid is decelerated in a duct, causing a rise in
pressure along the stream.
Major applications: Centrifugal Compressor and
the Ramjet.Analysis here will be restricted to One-dimensional Flow it is assumed that the Fluid Velocity, and the Fluid Properties, change only in the direction of the flow.
Fluid velocity is assumed to remain constant at a mean value across the cross-section of the duct.
Friction will not be analyzed Fundamentally, suitable efficiencies or coefficients being adopted to allow
for the departure from the ideal friction less case.
Further Explanation of variation of Nozzle-Areawith decreasing Pressure.
At low velocities the density is constant and therefore as the area gets smaller (Convergent Nozzle) the velocity must increase to keep ρVA constant. This is the case we are used to in our day to day lives. In reality, as velocity increases, the decreasing static pressure allows the air to expand. So as air accelerates through a convergent duct its volume gets bigger. At speeds closer to the speed of sound, the density is not a constant any more. At these speeds the fluid is sort of stretched out and less dense: the higher the velocity the lesser dense the fluid becomes. At this point we notice that the density and the velocity work in opposite directions in the quantity ρVA, that is, meanwhile more V brings ρVA higher, less ρ brings ρVA lower.
If in the nozzle we continue to make A smaller (convergent), eventually we will reach the point where ρ out-powers V in the expression ρVA and the velocity cannot go higher anymore. In other words, ρV reaches its maximum. Any increase in V will cause a decrease in ρ such as the quantity ρVA would be smaller and this is not possible, ρVA must be a constant. The value of V when this maximum happens is the speed of sound for this particular fluid and conditions. since the quantity ρV is at its maximum, the mass flow rate ρVA is at its maximum as well. In other words, it is impossible to increase the mass flow rate no matter what and the nozzle is said to be choked.
After the speed of sound is reached, if we increase A (divergent nozzle), V will continue to go up and ρ will continue to go down in such a way that ρVA will remain still constant. Effectively the fluid now behaves the opposite way, it will increase its velocity as the area increases and all because of the inverse relationship between the density and the velocity of the fluid.
|
Fluid Mechanics Lab
By : Asad Ali ArshadTo determine the velocity of fluid flowing through the circular tube using a pitot tube
(Pitot Tube Apparatus)
What is a Pitot Tube?
ØA Pitot tube, also known as Pitot probe, is a pressure measurement instrument used to measure fluid flow velocity.The pitot tube was invented by the French engineer Henri Pitot in the early 18th century. It is widely used to determine the airspeed of an aircraft, water speed of a boat, and to measure liquid, air and gas flow velocities in certain industrial applications.
The pitot tube is used to measure the local flow velocity at a given point in the flow stream and not the average flow velocity in the pipe or conduit.
Working Operation:
uThe basic pitot tube consists of a tube pointing directly into the fluid flow. As this tube contains fluid, a pressure can be measured; the moving fluid is brought to rest (stagnates) as there is no outlet to allow flow to continue. This pressure is the stagnation pressure of the fluid, also known as the total pressure or (particularly in aviation) the pitot pressure.
uThe measured stagnation pressure cannot itself be used to determine the fluid flow velocity (airspeed in aviation). However, Bernoulli's equation states:
Stagnation pressure = static pressure + dynamic pressure
Apparatus: Pitot tube apparatus
Procedure:
1. Place the pitot tube apparatus on the hydraulic bench.
2. Attach the pitot tube with hydraulic bench using pipe and quick release connectors.
3. Start the pump, and admit water to the tube by opening the flow control valve. adjust the flow rate in the tube using the flow control valve of apparatus and hydraulic bench simultaneously so that there are no air bubbles within the tube.
4. Change the flow rate and get different values.
5. For each flow rate allow conditions to become steady, measure and record h1 (static head) and h2 (stagnation head).
Fluid Mechanics Lab
By : Asad Ali ArshadTo compute the Reynolds’s Number and to observe the Laminar, Transitional and Turbulent Flow
(Osborne Reynolds’s Demonstration Unit)
Theoratical Background.
Reynold’s No:
ØThe Reynolds number (Re) is an important dimensionless quantity in fluid mechanics used to help predict flow patterns in different fluid flow situations.
ØIt is the ratio of inertial forces to viscous forces within a fluid which is subjected to relative internal movement due to different fluid velocities.
ØIt is used to predict the transition from laminar to turbulent flow.
Ølaminar flow occurs at low Reynolds numbers, where viscous forces are dominant, and is characterized by smooth, constant fluid motion.
turbulent flow occurs at high Reynolds numbers and is dominated by inertial forces, which tend to produce chaotic eddies, vortices and other flow instabilitie.
Procedure:
1. Lower the dye injector until it is seen in the glass tube.
2. Open the inlet valve and allow water to enter stilling tank.
3. Ensure a small overflow spillage through the over flow tube to maintain a constant level.
4. Allow water to settle for a few minutes.
5. Open the flow control valve fractionally to let water flow through the visualizing tube.
6. Slowly adjust the dye control needle valve until a slow flow with dye injection is achieved.
7. Regulate the water inlet and outlet valve until an identifiable dye line is achieved.
8. Measure the flow rate using volumetric method i-e collect the water from the outlet having
die in it in a volumetric tank and calculate the time with a stop watch.
9. Repeat the experiment by regulating water inlet and outlet valve to produce different flows
Fluid Mechanics Lab
By : Asad Ali Arshad![]() Experiment no 2 |
2. Viscometer.pptx
null
To Determine The Viscosity of Fluid Using Viscometer (Find The Viscosity of SAE-30 Lubrication Oil)
Viscometer:A viscometer (also called viscosimeter) is an instrument used to measure the viscosity of a fluid.It is used for those fluids whose viscosity does not change under varying flow conditions.
Rheometers must be used when the viscosity does change with flow conditions.
Viscometers usually work by comparing a stationary object and a fluid flow, or vice versa. Hence, a viscometer could be placed in a fluid flow or moved through a stationary fluid.
The flow must have a Reynolds number in the laminar region in order to record accurate values. The measure of the resistance is taken by measuring the drag resistance during relative motion through the fluid
ØThe viscometer consists of a rotating inner cylinder mounted on a vertical spindle at the top and free at the bottom.
ØThis inner cylinder is hollow and rotates inside another fixed outer cylinder of a larger diameter as shown in Fig.
ØThe space between the outer and inner cylinders is filled with the liquid for which the viscosity is to be measured.
ØThe inner cylinder is rotated by means of a vertically falling weight, which imparts rotational motion to the cylinder by using a pulley and a cord arrangement.
For a given weight, W, the speed of rotation of the inner cylinder is higher when the viscosity of the fluid is lower and vice versa.
Apparatus: Viscometer
Procedure: 1. Insert the fluid in the outer cylinder of unknown viscosity.
2. Attach the first weight (W = 100 grams) to the cord. This weight is the sum of the weight of the pan and the weight in the pan.
3. Release the brake and measure the time elapsed to hit the ground.
4. Note the distance covered by the pan.
5. Repeat the above procedure for the other four weights.
6. The viscosity of the fluid is now the average of the five values obtained from the above steps.
2. Attach the first weight (W = 100 grams) to the cord. This weight is the sum of the weight of the pan and the weight in the pan.
3. Release the brake and measure the time elapsed to hit the ground.
4. Note the distance covered by the pan.
5. Repeat the above procedure for the other four weights.
6. The viscosity of the fluid is now the average of the five values obtained from the above steps.
Fluid Mechanics Lab
By : Asad Ali Arshad![]() |
Bourden Tube Experiment |
1. Dead Weight Calibrator.pptx
null
To Calibrate a Bourdon Type Pressure Gauge Using a Dead Weight Pressure Gauge Calibrator
Theoretical Background
1. Calibration: To check error with comparison to some standard device is called calibration.
2. Absolute Pressure (Pabs): The pressure that is taken with reference to absolute zero is called absolute pressure, and at absolute zero there is a perfect vacuum.
3. Gauge Pressure (Pg): The pressure that is taken with reference to atmospheric pressure is called gauge pressure. It may be positive or negative depending upon whether we take (Pg) above the atmospheric pressure or below the atmospheric pressure. Gauge pressure is always measured with atmospheric pressure, that is why when gauge pressure is at atmospheric pressure it results zero.
Pabs = Patm + Pgau
Bourdon Tube Pressure Gauge:
uThe bourdon tube pressure gauge is the most common type used to measure fluid pressure because it is reliable, inexpensive and relatively simple.
uThe bourdon tube is a curved tube closed at one end, which is attached to a spring-loaded mechanism that is itself attached to the gauge’s needle.
uThe port of the gauge is attached to the location in the system where you’re measuring pressure.
As pressure increases within the bourdon tube, the metal tube starts to straighten, and as it does, it tugs on the lever attached to the needle.
Apparatus: Dead Weight Tester
Procedure:
1. Remove the piston from unit.2. Close valve V1 and open valve V2.
3. Fill cylinder with oil.
4. Now close valve V2.
5. Put piston back in position with V1 and V2 in close position.
6. Read out pressure value on gauge and compare it with theoretical results.
7. Repeat the experiment by adding weights.
5 Most Important Skills for a Mechanical Engineer to Succeed..
By : Asad Ali Arshad5 Most Important Skills for a Mechanical Engineer to Succeed..
Hello and welcome to my blog.
Today we are going to talk about five skills every mechanical engineer should have in order to succeed.Mechanical engineering is the branch of engineering that involve the design production and operation of machinery it is one of the oldest and broadest of engineering disciplines. This field requires an understanding of core area including Mechanics, Dynamics, Thermodynamics, Material Science, Electricity and much more. It is very important for a mechanical engineers to posses certain qualities and skills here we are providing the five most important skills that mechanical engineer should have in order to succeed.
Problem Solving
A big part of mechanical engineer job is solving problems using mechanical or thermal devices. Mechanical engineers need to be strong and analytic thinker who are capable of solving problems brought them by clients and employers.
Creativity
![]() |
Creativity |
Mechanical engineering involves developing and designing products which range from batteries to electric generator to medical devices inventing products involve a lot creativity the creative mind is essential for this kind of work.
Communication Skills
![]() |
Communication Skills |
Often mechanical engineers develop a product for a client they may have to explain complex machines or devices to people who are not familiar with the mechanical engineering. They have to be able to explain their ideas clearly and effectively and this takes strong communication skills.
Team Work
![]() |
Teamwork |
Mechanical engineering involves a lot of team work Engineers often working groups to invent technologies and solve problems they might work with people who are not mechanical engineers such as computer scientist or architect They therefore need to be able to work with a diverse team of people to solve problems.
![]() |
Math Skills |
Lastly math skills mechanical engineers need to be comfortable using math to solve problems the math skills required in mechanical engineering include calculus and statistic I need to be able to apply these skills to analyze problems and design solutions.
Thanks for reading....
Thermodynamic
By : Asad Ali ArshadChapter no 7: Entropy
Entropy may be understood as the measure of disorder within the microscopic system.
chapter 7.pdf
null
Book:
Thermodynamics: An Engineering Approach by Yunus A.Cengel, Michael A.Boled 5th Edition
In this chapter we will discuss the following topic and these topic are discussed in detail in the above slides.
- The inequality of Clausius (for irreversible cycle and for reversible cycle).
- Entropy A property of the system
- Internally Reversible Isothermal Heat Transfer Processes
- The increase of entropy priciple
- Some remarks of about entropy
- Problems
- Entropy of water
- Entropy change of pure substances
- Isentropic process
- Property diagrams involving entropy
- What is Entropy?
- Entropy change of solids and liquids
- Entropy change of ideal gases
- Problems
Engineering Mechanics Lab
By : Asad Ali Arshad![]() |
Engineering Mechanics Lab |
Rack-Pinion animation.mp4
null
Worm Gear.mp4
null
Cam and Follower Mechanism in Engine - Magic Marks_2.mp4
null
Cam and Follower.pptx
null
Rack-Pinion animation.mp4
null
How Bevel Gears Work.mp4
null
Gear Train Mechanism.pptx
null
Mechanics of Material
By : Asad Ali Arshad![]() |
Mechanics of Material Chapter no 6 |
Mechanics of Material
6_shearing_stresses.pdf
null
Chapter no 6
Shearing Stress in Beams and Thin Walled Members
In this we will discussed the following topic and these topics are discussed in detail in the above given slides.
Introduction
Transverse loading applied to a beam
results in normal and shearing stresses in
transverse sections.
Distribution of normal and shearing
stresses satisfies.
When shearing stresses are exerted on the
vertical faces of an element, equal stresses
must be exerted on the horizontal faces.
Longitudinal shearing stresses must exist
in any member subjected to transverse
loading.
- Shear on a horizontal face of a beam
- Solved Example Problem 6.1
- Determination of Shearing Stress in a Beam
- Shearing Stress in Common Types of a Beam
- Solved Example Problem 6.2
- Shearing Stress in Thin Walled Members
Mechanics of Material
By : Asad Ali Arshad![]() |
Mechanics of Material Chapter no 5 |
Chapter no 5 : Mechanics of Material
Analysis and Designs of Beam for Bending
In the above slides we will discussed this chapter in detail and solved some of the conceptual questions.
We will cover the following topics of this chapter
A safe design requires that the maximum normal stress be
less than the allowable stress for the material used. This
criteria leads to the determination of the minimum
acceptable section modulus.
Among beam section choices which have an acceptable
section modulus, the one with the smallest weight per unit
length or cross sectional area will be the least expensive
and the best choice
We will cover the following topics of this chapter
Introduction to this chapter
Objective - Analysis and design of beams
• Transverse loadings of beams are classified as
concentrated loads or distributed loads
• Applied loads result in internal forces consisting
of a shear force (from the shear stress
distribution) and a bending couple (from the
normal stress distribution)
• Normal stress is often the critical design criteria
![]() |
Bending moment |
Requires determination of the location and
magnitude of largest bending moment.
Classification of Beams
Shear and Bending Moment Diagram
- Determination of maximum normal and shearing stress requires identification of maximum internal shear force and bending couple.
- Shear force and bending moment at a point determined by passing a section through the beam and applying an equilibrium analysis on the beam portions on either side of the section.
Solved Sample Problem 5.1
Solved Sample Problem 5.2
Relation between load shear and bending moment
Solved Sample Problem 5.3
Solved Sample Problem 5.4
Design of prismatic beams for bending
The largest normal stress is found at the surface where the
maximum bending moment occurs.
![]() |
Bending Moment |
less than the allowable stress for the material used. This
criteria leads to the determination of the minimum
acceptable section modulus.
![]() |
Section Modulus |
chap-5.pdf
null
Among beam section choices which have an acceptable
section modulus, the one with the smallest weight per unit
length or cross sectional area will be the least expensive
and the best choice
Solved Sample Problem 5.8
For more detail download the above slides..
Hitec Mechanical Engineering
Mechanical Engineeirng Hitec Mechanical Engineering As we know Mechanical Engineering is the branch of engineering dealing with the des...
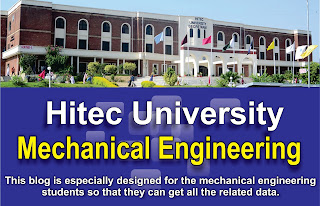